Полирањето може да се подели на грубо полирање, средно полирање и фино полирање. Грубото полирање е процес на полирање на површина со или без тврдо тркало, кое има одреден ефект на брусење врз подлогата и може да отстрани груби траги. Средното полирање е понатамошна обработка на грубо полирани површини со употреба на тврди тркалца за полирање. Може да ги отстрани гребнатинките оставени од грубото полирање и да произведе умерено сјајна површина. Финото полирање е последниот процес на полирање, со употреба на меко тркало за полирање и добивање на светла површина како огледало. Има мал ефект на брусење врз подлогата.
Ⅰ.Полирачка за полирање
Полирачките тркала се направени од различни ткаенини, а нивните структурни форми главно вклучуваат следново:
1. Вид на шев: Се прави со шиење парчиња ткаенина заедно. Методите на шев вклучуваат концентричен круг, радијален, радијален лак, спирален, квадратен итн. Според различната густина на шиење и ткаенините, може да се направат тркала за полирање со различна тврдост, кои главно се користат за грубо полирање.
2. Незашиени: Има два вида: дисков тип и крилов тип. Сите се склопуваат во меки тркала со употреба на платнени листови, специјално дизајнирани за прецизно полирање. Крилата имаат подолг век на траење.
3. Преклопување: Се формира со преклопување на тркалезни парчиња ткаенина во два или три превиткувања за да се формира „форма на торба“, а потоа наизменично нивно редење едно врз друго. Ова тркало за полирање е лесно за складирање на средства за полирање, има добра еластичност, а исто така е погодно и за воздушно ладење.
4. Тип на збрчкање: Исечете ја ролната од ткаенина на 45 аголни ленти, зашијте ги во континуирани, наклонети ролни, а потоа завиткајте ја ролната околу жлебен цилиндар за да формирате збрчкана форма. Центарот на тркалото може да биде вграден со картон за да се овозможи тркалото да се вклопи со вратилото на машината. Може да се инсталираат и челични тркала со вентилација (оваа форма е подобра). Карактеристика на ова тркало за полирање е добра дисипација на топлина, погодно за брзо полирање на големи делови.
Ⅱ. Средство за полирање
1. Паста за полирање
Полирната паста се прави со мешање на абразив за полирање со лепило (како што се стеаринска киселина, парафин итн.) и може да се купи на пазарот. Нејзината класификација, карактеристики и употреба се прикажани на следната слика.
Тип | Карактеристики | Цели |
Бела паста за полирање
| Направено од калциум оксид, магнезиум оксид и лепило, со мала големина на честички, но не остри, склони кон атмосферски влијанија и влошување при долгорочно складирање. | Полирање на помеки метали (алуминиум, бакар, итн.) и пластични материјали, исто така се користи за прецизно полирање |
Црвена паста за полирање | Направено од железен оксид, оксидирана лажица и лепило итн., Умерена тврдост | Полирање делови од општ челик, за алуминиум, бакар и други деловиГрубо фрлање предмети |
Зелена паста за полирање | Користење на материјали како што се Fe2O3, алумина и лепила направени со силна способност за мелење | Полирање на тврд легиран челик, слој за пат, не'рѓосувачки челик |
2. Раствор за полирање
Абразивот за полирање што се користи во течноста за полирање е ист како оној што се користи во пастата за полирање, но првиот се користи на собна температура во течна емулзија од масло или вода (не треба да се користат запаливи материјали) за да се замени цврстиот лепак во пастата за полирање, што резултира со течен агенс за полирање.
Кога се користи раствор за полирање, тој се прска врз тркалото за полирање со кутија за снабдување под притисок, кутија за снабдување со високо ниво или пумпа со пиштол за прскање. Притисокот на кутијата за напојување или моќноста на пумпата се одредуваат од фактори како што се вискозитетот на растворот за полирање и потребната количина на снабдување. Поради постојаното снабдување со раствор за полирање по потреба, може да се намали абењето на тркалото за полирање. Нема да остави премногу средство за полирање на површината на деловите и може да ја подобри ефикасноста на производството.
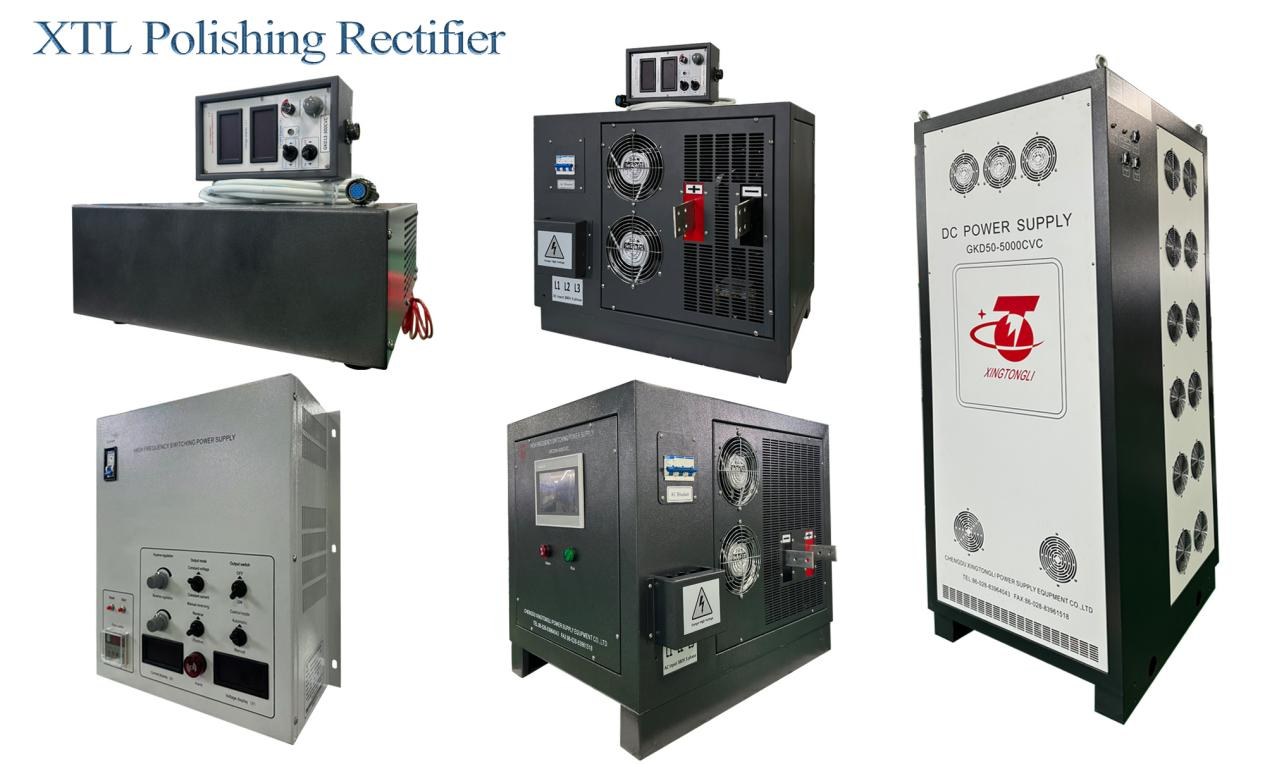
Време на објавување: 29 ноември 2024 година